Teil II – Rauheit
Im ersten Teil dieses Beitrags (Newsletter 03 / 2018_ Teil I – Rauheit) wurden die Einflüsse des Schleifabtrags pro Kopf sowie der Kornfolge auf die Rauheit näher erläutert. In diesem zweiten Teil steht nun der Einfluss der Maschinenkonfiguration auf die Oberflächenqualität im Fokus.
Das signifikanteste Unterscheidungsmerkmal von Breitbandschleifmaschinen sind die Schleifköpfe, die in Anzahl und Typ variieren können. Steinemann setzt auf ein grosses Spektrum an Möglichkeiten und setzt daher Schleifanlagen ein, die entweder nur einen Kopf, oder auch bis zu zwölf Schleifköpfe aufweisen können. Dieser Beitrag zeigt auf, warum diese Varianz ihre Berechtigung hat.
Abbildung 1: Eine Kalibrier-Schleifmaschine mit vier Köpfen
In Abbildung 1 ist eine Kalibrierschleifmaschine mit zwei Stationen zu sehen (KK-Maschine). Die zwei Stationen (links/rechts) sind jeweils mit zwei Aggregaten (oben/unten) bestückt. Das Herzstück eines solchen Schleifkopfs als Kalibrier-Aggregat ist die Kontaktwalze.
Abbildung 2 zeigt schematisch diese Kontaktwalze im Eingriff. Bei einem Abtrag von 0.2 mm während des Kalibrierschliffs (K) ist die Kontaktzone des Schleifbandes (Durchmesser 455 mm) etwa 19 mm lang. Auf diesen 19 mm greift das Band in die Platte ein, entfernt das Deckschichtmaterial und transportiert es in Richtung der Absaugung. Die Kontaktzone beim Feinschliff (N) ist mit 55 mm fast drei Mal länger (siehe Abbildung 3).
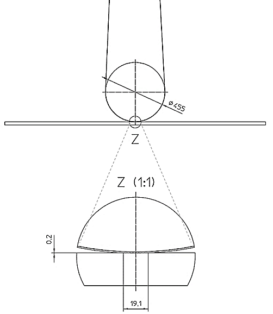
Abbildung 2: Berechnung der Kontaktfläche beim Kalibrierschliff
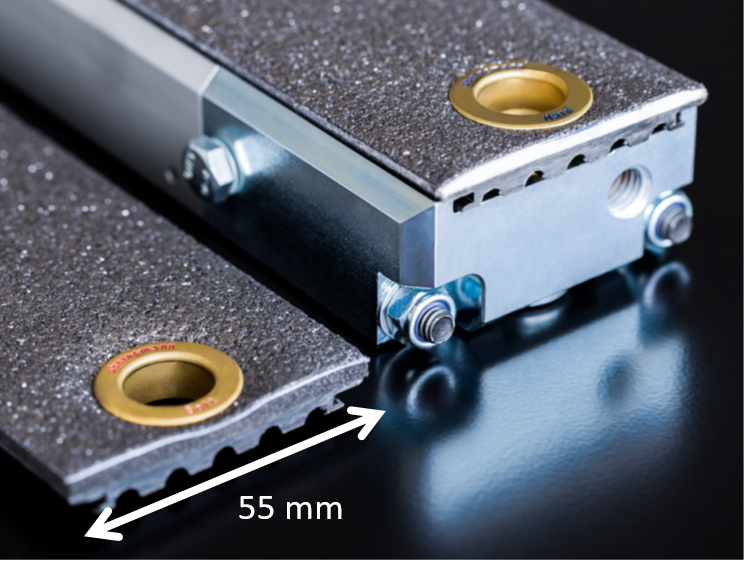
Abbildung 3: Steinemann Sprint-Inserts; Kontaktfläche beim Feinschliff
Aufgrund der grösseren Kontaktzone ist im Feinschliff eine grössere Fläche Schleifband im Eingriff. Eine grössere Bandfläche bedeutet auch immer, dass eine grössere Anzahl Schleifkörner beteiligt ist. Dabei hat die Anzahl der Schleifkörner einen grossen Einfluss auf den Schleifprozess: Sind z. B. nur vier Körner im Eingriff, wird die gesamte Schleifkraft auf diese vier Körner verteilt – es entstehen vier tiefe Kratzer in der Oberfläche. Sind – bei gleicher Schleifkraft – hingegen acht Körner beteiligt, verteilt sich die Last auf diese acht. Das Resultat sind acht Kratzer, die aber weniger tief sind.
Den Nachweis für diese theoretische Betrachtung liefern die Abbildung 4 und 5. Abbildung 4 zeigt die Oberfläche einer MDF-Platte nach einem P80-Schliff mit den Kalibrieraggregaten, Abbildung 5 nach dem Feinschliff mit gleicher Körnung. Zu sehen ist, dass die Plattenoberfläche nach dem Kalibrierschliff deutlich rauer ist als ein P80-Finish nach dem Feinschliff; die Kratzer in Abbildung 4 sind deutlich tiefer und kürzer als die in
Abbildung 5.
Übrigens: Steinemann hat gute Erfahrungen damit gemacht, im letzten Kalibrierschliff-Kopfpaar und im ersten Feinschliffaggregat die gleiche Korngrösse zu verwenden. Aufgrund der Charakteristik eines Feinschliffaggregates ist die Oberfläche nach dem ersten Feinschliff weniger rau als bei gleicher Korngrösse nach dem Kalibrierschliff; zudem ist die Korngrösse im ersten Feinschliffaggregat grob genug, um die Rattermarken aus dem Kalibrierschliff zu entfernen.

Abbildung 4: Oberflächenbeschaffenheit einer MDF-Platte nach dem Kalibrierschliff (K)

Abbildung 5: Oberflächenbeschaffenheit einer MDF-Platte nach dem Feinschliff (N)
Des Weiteren gilt:
- Je höher die Anzahl der Kalibrierköpfe ist, desto höher ist die Kapazität/Schleifgeschwindigkeit, da mehr Material in kürzerer Zeit entfernt werden kann.
- Eine höhere Anzahl von Feinschleifköpfen führt zu einer besseren Beschaffenheit der Plattenoberfläche, da eine optimale Kornfolge gewählt werden kann (siehe Tabelle 1).

Fazit: Die Anzahl von Kalibriereinheiten definiert die Kapazität einer Schleiflinie, die Anzahl an Feinschleifaggregaten definiert die Rauheit einer Platte.
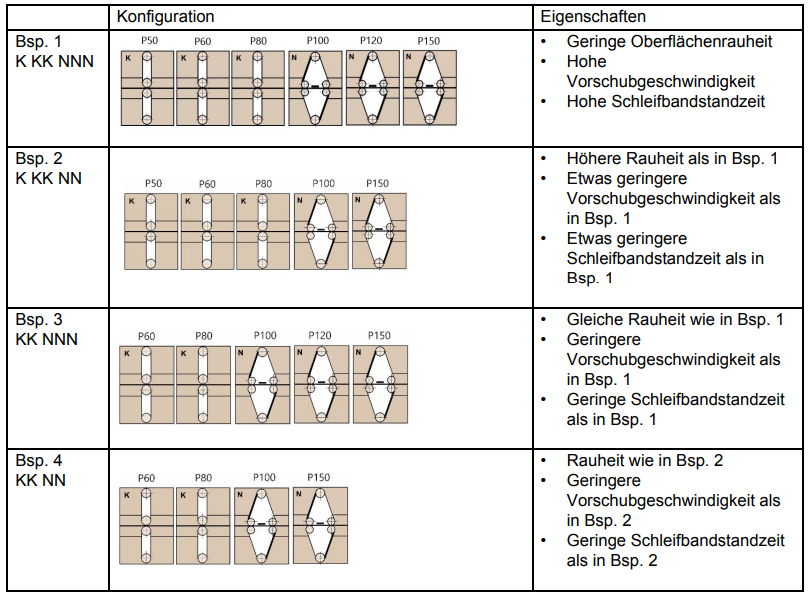
(K = Kalibrierschliff; N = Feinschliff; P = Korngrösse)