Einleitung
Das Dichteprofil ist ein wesentliches Merkmal, um die physikalischen und mechanischen Eigenschaften einer Platte zu bestimmen. Dabei zeigt das Dichteprofil, gemessen senkrecht zur Plattenoberfläche, die verschiedenen Bereiche der Dichte über die gesamte Platte an. Je nach Ausprägung hat das Dichteprofil einen entscheidenden Einfluss auf die Oberflächenrauheit sowie auf die Oberflächenqualität nach dem Schleifen.

Abbildung 1: Dichteprofil senkrecht zur Plattenoberfläche
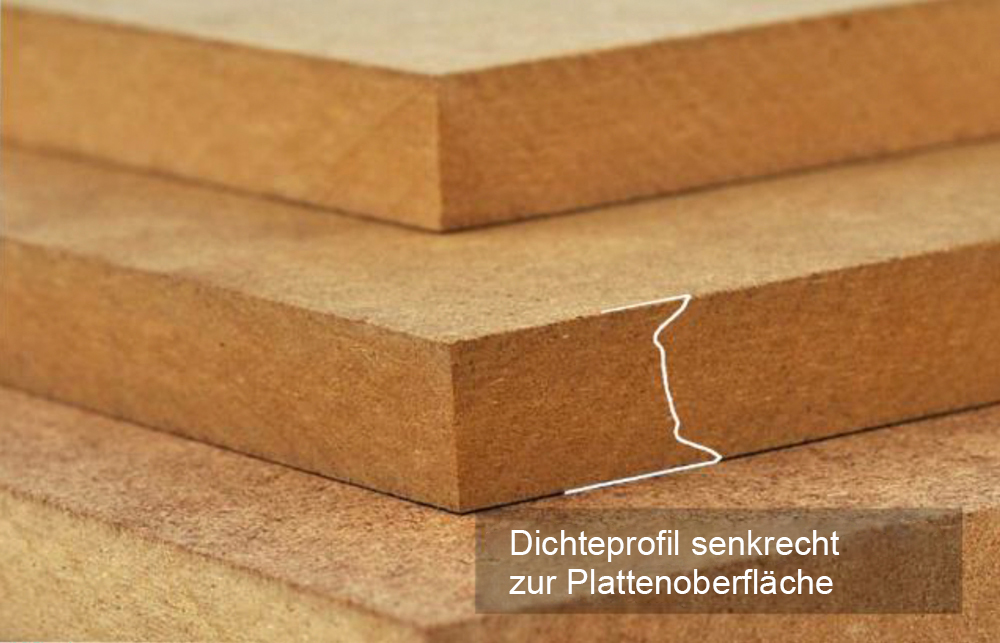
Abbildung 2: Der Dichteverlauf senkrecht zur Oberfläche einer Spanplatte
Abbildung 1 zeigt ein typisches Dichteprofil senkrecht zur Plattenoberfläche. Die Spitzen links und rechts im Kurvenverlauf zeigen die Dichte in der oberen und unteren Decklage (siehe auch Abbildung 2). Der Plattenhersteller wünscht eine hohe Dichte in der Decklage und eine geringe Dichte in der Kernlage. Das ist die einzige Möglichkeit, eine Platte mit hohen Festigkeitseigenschaften und geringem Gewicht herzustellen.
Kurzer Exkurs

Abbildung 3: Verschiedene Arten von (Press-)Spanplatten
In Abbildung 3 sind verschiedene Arten von Pressspanplatten abgebildet. Sie unterscheiden sich durch die Anzahl der Lagen. Je mehr Lagen es gibt, desto größer ist der Unterschied in der Dichte von Decklage und Kernlage.
Je kleiner die Späne in der Decklage sind, desto größer ist die spezifische Oberfläche der Späne. Das führt zu einem höheren Harzverbrauch mit folgenden Konsequenzen:
- höhere Produktionskosten für die Decklage
- höheres Gewicht
- höhere Dichte
- geschlossenere/glattere Oberfläche
Je größer die Späne, desto höher ist die Porosität aufgrund der höheren Luftmenge um die Partikel herum.
Eine andere Dichte in der MDF-Platte kann nur mit dem Pressprogramm der Heißpresse erreicht werden.

Abbildung 4: Doppelbandpresse (Siempelkamp 2008)
Das Pressprogramm bestimmt die Temperatur der Heizplatten, den Druck der Presse und die Geschwindigkeit der Stahlbänder. Je schneller die Stahlbänder laufen, desto niedriger ist der Druck-Zeit-Faktor und desto schneller ist die Produktion. Wie auf Abbildung 4 zu sehen, wird die Spanmatte auf der linken Seite eingeführt. Die Oberfläche der Matte wird mit den Heizplatten erhitzt (konduktive Wärmeübertragung). Wasser in der oberen Lage verdampft, sodass der Gasdruck steigt. Heißer Dampf beginnt aus den Hohlräumen der Matte in Richtung des Gasdruckgefälles in die Mitte der Platte zu fließen. Wenn der Dampf auf kältere Späne trifft, kondensiert er wieder zu ungebundenem Wasser, wodurch Kondensationsenergie entsteht.
Dadurch steigt die Temperatur in der Mitte einer Platte auf bis zu 100 °C.
Wenn die Oberfläche trocken ist, kann mittels konduktiver Wärmeübertragung Wärme in die Kernlage gelangen. Während die Temperatur in der Plattenmitte steigt, verdampft erneut ungebundenes Wasser und der Gasdruck steigt (Abbildung 5). Ist der Gasdruck höher als die interne Haftfestigkeit nach dem Pressen, bläht sich die Platte auf (Blasen). Dies kann jedoch durch die Reduzierung der Produktionsgeschwindigkeit verhindert werden.

Abbildung 5: Verteilung des Gasdrucks aus einer 16-mm-Spanplatte (Thoemen, Walther 2010)
Versuchsreihe und Ergebnisse
In diesen Versuchen soll der Einfluss der Dichte auf die Rauigkeit einer geschliffenen MDF-Platte genauer untersucht werden. Zu diesem Zweck wurden 7,20 mm dicke MDF-Platten geschliffen auf
- 6,95 mm
- 6,80 mm
- 6,50 mm
- 6,25 mm und
- 5,60 mm
Geschliffen wurde mit der Korngröße P150.
Das Dichteprofil aller Platten wurde gemessen. Die Ergebnisse sind in Abbildung 7 dargestellt.

Abbildung 6: Rechte Seite des Dichteprofils von geschliffenen Platten
Es wird nur die rechte Seite des Dichteprofils gezeigt, da die Platten nur auf einer Seite geschliffen wurden. Der Kreis markiert die Stelle mit der höchsten Oberflächendichte. Wie deutlich zu erkennen ist, nimmt die Dichte bei stärkerem Schleifen ab.
Abbildung 7 zeigt die Beziehung zwischen Oberflächendichte und Rauigkeit. Je höher die Dichte, desto geringer (also besser) ist die Rauigkeit.

Abbildung 7: Dichteprofil der geschliffenen Platten (nur eine Seite)
Das lässt sich durch die Porosität des Materials erklären. Je geringer die Dichte, desto höher die Porosität.
Abbildung 8 bis Abbildung 13 zeigen die Oberfläche der jeweils geschliffenen Platte. Auf der ersten Abbildung sind auf der Oberfläche die Kratzspuren der Bandkörnung zu erkennen. Mit zunehmender Schleiftiefe wird die Oberflächenstruktur jedoch immer mehr durch die Porosität der Platte selbst und nicht durch das Schleifband bestimmt.

Abbildung 8: Oberfläche der 6,95-mm-Platte

Abbildung 9: Oberfläche der 6,80-mm-Platte

Abbildung 10: Oberfläche der 6,55-mm-Platte

Abbildung 11: Oberfläche der 6,25-mm-Platte
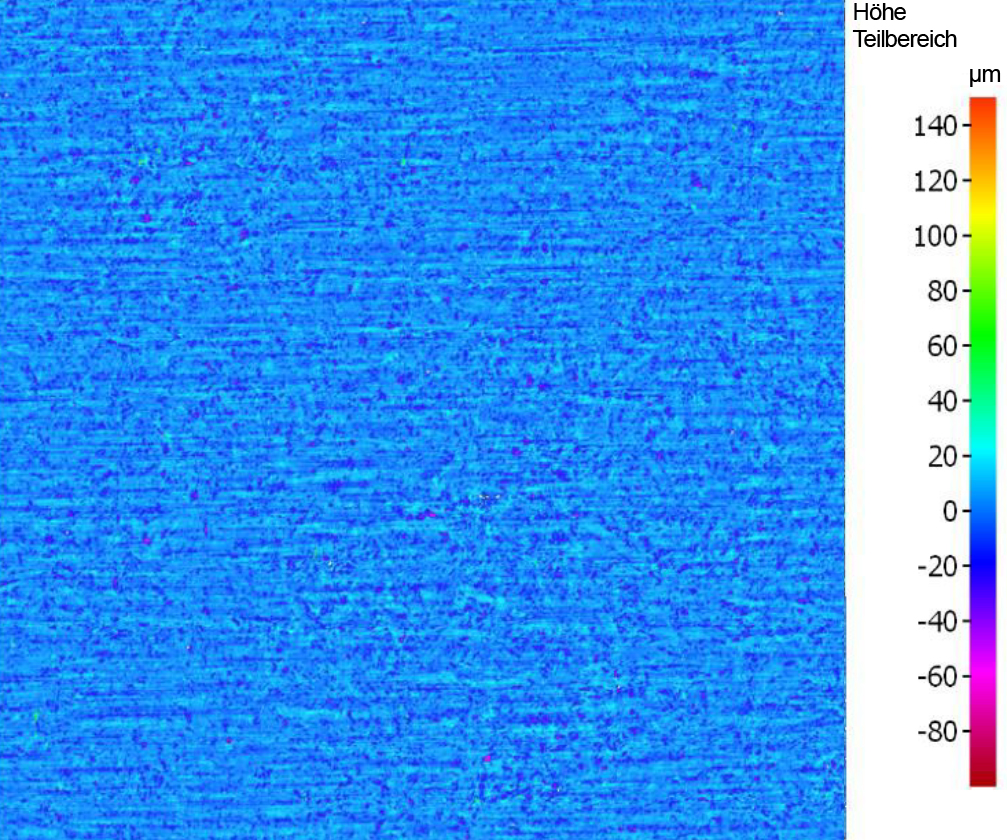
Abbildung 12: Oberfläche der 5,93-mm-Platte

Abbildung 13: Oberfläche der 5,60-mm-Platte
Zusammenfassung
Je geringer die Dichte in der Oberfläche ist, desto geringer ist die Oberflächenqualität. Trotz Verwendung derselben Korngröße nimmt die Rauigkeit der Oberfläche bei abnehmender Oberflächendichte zu. Das ist wichtig für den Kunden. Schleift dieser zu tief, gelangt er immer mehr in den Bereich der Platte mit geringerer Dichte und die Oberfläche wird rauer. Dasselbe kann geschehen, wenn der Kunde auf einer Seite mehr als auf der anderen abschleift. In diesem Fall muss er seine Schleifmaschine neu einstellen.
Normalerweise haben alle Spanplatten an der unteren Oberfläche eine höhere Dichte als an der oberen. Das liegt am Herstellungsverfahren. Kleine Vibrationen des Transportsystems in der Formstation bewirken, dass die feineren Späne zur unteren Lage der Matte wandern. Das führt zu einer höheren Dichte in der unteren Oberfläche. Aufgrund des selbstausrichtenden Transporttischsystems der Schleifmaschinen, wählt die Platte auf ihrem Weg durch die Maschine den einfachsten Weg. Dadurch werden die Plattenteile mit hoher Dichte weniger geschliffen als diejenigen mit geringerer Dichte. Im Extremfall kann dadurch die Dichtedifferenz zwischen oberer und unterer Oberfläche nach dem Schleifen sogar höher sein, was zu großen Unterschieden in der Rauigkeit von oberer und unterer Oberfläche führt.
Sollte der Kunde Probleme mit unterschiedlichen Oberflächendichten haben, schafft das Transporttischsystem der satos TSQ Abhilfe. Hier sind die unteren Transporttische an der Maschine fixiert.
Das ermöglicht dem Bediener, das Transportsystem so auszurichten, dass an der Unterseite mehr als an der Oberseite geschliffen wird.